強度や耐久力をシミュレーションしたい
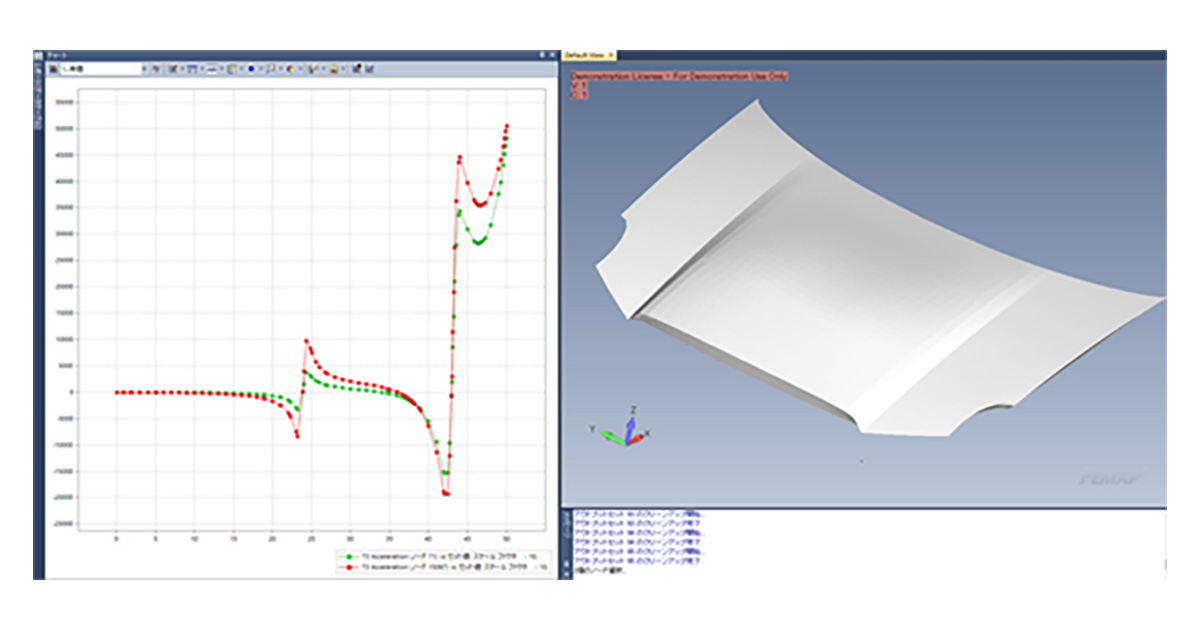
製造業や建設業、さらには航空宇宙や自動車業界において、製品や構造物の強度や耐久性を確保することは非常に重要です。これらの要素が不十分であれば、製品の失敗や事故につながり、企業の信頼性や経済的損失を引き起こす可能性があります。そのため、強度や耐久性をシミュレーションし、実際の使用条件での挙動を予測することが不可欠です。
このページでは、強度や耐久性をシミュレーションする重要性や方法、さらにCAE解析の導入について詳しく解説します。
強度や耐久性をシミュレーションする重要性
① 製品開発の迅速化
製品の強度や耐久性を事前にシミュレーションすることで、設計段階での問題を早期に発見し、修正を行うことができます。これにより、物理的な試作や実験にかかる時間とコストを大幅に削減し、開発プロセスをスピードアップさせることが可能です。
② 安全性の確保
製品や構造物が実際に使用される環境では、さまざまな外部要因が影響を与えます。強度や耐久性をシミュレーションすることで、これらの要因に対する耐性を評価し、安全性を確保できます。特に航空機や自動車の設計においては、事故を未然に防ぐためにこのプロセスが欠かせません。
③ コスト削減
シミュレーションを通じて設計の最適化が図られることで、無駄な材料の使用を避けることができます。また、実際の物理試験を減らすことができるため、開発コスト全般を削減できます。最終的には、競争力のある製品を市場に迅速に提供できることが企業の利益につながります。
強度や耐久力をシミュレーションする方法
方法① 物理的耐久試験(衝撃試験)
実際に対象物に衝撃を与え、その耐久性を評価する手法です。例えば、落下試験や衝撃試験機を用いた試験がこれに該当します。これにより、実際の使用条件での物理的な反応を観察し、耐久性を測定します。
方法② 模型実験
模型を作成し、実際の構造物の縮小版を用いて実験を行います。この手法では、模型を使用して、特定の条件下での挙動を観察し、設計上の問題点や改善点を特定します。これは、風洞実験や振動台試験などでよく使用されます。
方法③ 疲労試験
疲労試験は、材料が繰り返しの応力や荷重を受けた際に、その耐久性を測定するための実験です。特に、構造物や部品が動的な条件下での耐久性を評価するために重要な試験です。このテストでは、実際に材料や部品に繰り返しの負荷をかけ、どの時点で破壊や損傷が発生するかを観察します。
方法④ CAE解析
CAE(Computer-Aided Engineering)解析は、上記の物理試験に代わる、または補完する強力な手法です。CAE解析では、有限要素法(FEM)を用いて、材料や構造物の強度や耐久性をシミュレーションします。この手法は、複雑な構造に対しても高精度な解析が可能であり、特に早期の設計段階での問題発見や改良に役立ちます。実験では把握しきれない詳細な挙動を分析することができるため、非常に有用です。
シミュレーションの流れ
まず、シミュレーションの目的や必要な評価項目を明確に定義します。強度や耐久性を評価する対象物の特性、使用条件、必要な解析精度などを検討します。
対象物のCADデータや設計図を基に、シミュレーション用のモデルを作成します。この際、メッシュ生成や要素分割が行われ、シミュレーションの精度を高めるための工夫が必要です。
シミュレーションを行うためには、外部からの荷重や温度、拘束条件などの境界条件を設定する必要があります。これにより、実際の使用環境を再現します。
設定したモデルと境界条件を基に、シミュレーションを実行します。この過程で得られるデータは、応力分布や変形量など、強度や耐久性に関する重要な情報となります。
解析結果を基に、設計や材料の改良が必要かどうかを評価します。結果は報告書としてまとめられ、関係者と共有されます。必要に応じて、再設計や追加のシミュレーションが行われます。
まとめ
強度や耐久性のシミュレーションは、製品開発や設計において不可欠なプロセスです。シミュレーションを通じて、早期に問題を発見し、コストを削減しながら安全性を確保することが可能になります。特にCAE解析は、強度や耐久性を評価するための最適な手法であり、多角的な視点からの解析が可能です。
お気軽にご相談ください
強度や耐久性のシミュレーションに関するご質問やご相談がございましたら、お気軽にお問い合わせください。
豊富な経験を持つ解析エンジニアがニーズに合った最適なソリューションを提案します。