製品不良の原因を調査したい
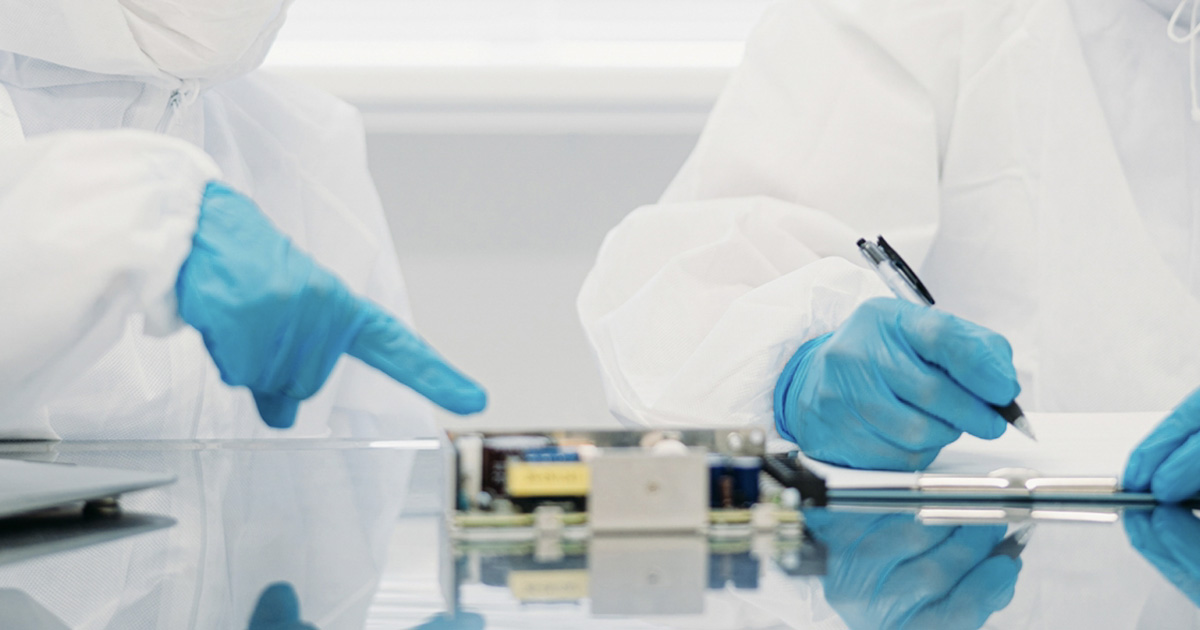
製造業において、製品不良の原因を特定し、再発防止策を講じることは非常に重要です。しかし、製品不良の原因は多岐にわたり、その特定が難しいケースが少なくありません。
特に、複雑な製品やプロセスでは、表面的な問題だけではなく、設計や材料、製造工程の細部に潜む根本的な問題を見つけ出すことが求められます。
このページでは、製品不良の原因を調査する際の課題と、効果的な調査方法について解説し、CAE(Computer-Aided Engineering)受託解析を活用した原因特定の有効性についてご紹介します。
製品不良の原因の特定が難しい理由
理由① 複雑な要因が絡み合う
製品不良の原因を特定することが難しい理由のひとつに、製造工程が多段階にわたり、各プロセスが複雑に絡み合っている点が挙げられます。例えば、材料の選定、設計の段階から製造プロセス、さらには外部環境や使用条件に至るまで、複数の要因が不良の原因となる場合があります。それぞれの要因が複雑に関連しているため、単純に「ここが原因」と特定することが困難です。
理由② 目に見えない内部要因
不良の原因が、製品の内部構造や微細な物理的・化学的変化に起因することもあります。こうした要因は、通常の目視検査や簡易的な検査装置では確認できないことが多く、詳細な解析や高度な技術が必要となります。また、使用される材料の微細な品質差異や、製造環境の温度や湿度など、外部から直接観察できない変動が原因となることもあります。
理由③ 長期間で発生する不良
製品が市場に出回った後、一定の使用期間が経ってから不良が発生するケースもあります。このような不具合は、短期間の製品テストでは発見しにくく、長期間使用した際にのみ現れる問題です。こうした場合、製造プロセスだけでなく、製品の設計段階でのシミュレーションや、耐久試験などの対応が必要になります。
製品不良の原因を調査する方法
製品不良の原因を調査するには、さまざまなアプローチが存在します。ここでは、主な調査方法をいくつか紹介します。
方法① 視検査と初期分析
まず最初に行うべきは、目視検査や初期分析です。肉眼で確認できる不良や、顕微鏡などの基本的な装置を用いた検査により、異常の外観や形状の変化を確認します。これは基本的なステップですが、簡単な不良や表面的な問題を特定する際に有効です。
方法② 不良発生時の条件を分析
不良が発生した状況や条件を詳細に記録し、原因を探る手法です。例えば、どのラインで不良が発生したのか、どのような環境条件や作業者によって製造されたのか、またどのロットの材料が使用されたのかなどを調査します。この情報を基に、問題が発生したプロセスや段階を絞り込むことが可能です。
方法③ 非破壊検査
製品を壊さずに内部の異常を確認するために、X線や超音波などの非破壊検査技術が活用されます。この方法は、目に見えない内部のクラックや気泡、異常な密度変化などを検出する際に有効です。特に高価な部品や製品に対しては、破壊せずに原因を調査できるため、非破壊検査が好まれることが多いです。
方法④ 材料解析
製品の不良が材料に起因する可能性がある場合、材料自体の物理的・化学的な解析を行います。特に、材料の組成、硬度、耐久性、腐食性などを調べることで、不良の原因を特定できます。例えば、材料の混合比率に問題があった場合や、使用環境に適さない材料が選定されていた場合に有効です。
方法⑤ CAE解析によるシミュレーション
CAE(Computer-Aided Engineering)を活用した解析は、製品不良の原因特定において非常に有効です。特に、製品設計や製造プロセスにおける物理的な応力、変形、温度変化などをシミュレーションすることで、実際の使用環境や製造過程を仮想的に再現し、どの段階で不良が発生しているかを明らかにすることが可能です。
CAEは、高度な解析能力を持ち、細かい部分での製品の挙動を正確に把握できるため、従来の手法では特定できなかった微細な問題や複合的な要因を明らかにします。CAE解析の結果を基に、設計の見直しやプロセスの改善を行うことで、再発防止策を講じることができます。
CAE受託解析までの流れ
まず、発生している不良の具体的な現象や問題点についてヒアリングを行います。不良が発生した条件や環境、製造プロセスに関する詳細な情報を提供することで、解析の方向性を決定します。
次に、製品の設計データや材料データ、製造条件など、解析に必要なデータを収集します。この段階では、収集したデータをCAEソフトウェアに適した形に前処理する作業も行われます。
収集したデータを基に、CAEソフトウェアを使用してシミュレーションを実施します。応力解析、熱解析、流体解析など、製品や問題に応じた様々な解析手法を用いて不良の発生原因を明らかにします。。
解析の結果を基に、不良の原因を特定し、報告書として提出します。また、再発防止のための具体的な対策案や改善提案も併せて提示します。設計変更や材料の見直し、製造プロセスの改善など、具体的な対策を講じることが可能です。
CAE解析の注意点
注意点① データの品質
CAE解析の精度は、入力するデータの品質に大きく依存します。設計データや材料特性、製造条件が正確でなければ、解析結果も正確なものにはなりません。したがって、正確なデータの提供が解析成功のカギとなります。
注意点② シミュレーション結果の解釈
CAEのシミュレーション結果は、現実の問題を反映していますが、必ずしも全ての状況を完全に再現できるわけではありません。結果を正しく解釈し、他の検証手法と組み合わせて最終的な判断を行うことが重要です。
まとめ
製品不良の原因を特定することは、製品の品質向上と企業の競争力強化において非常に重要です。
製造工程が複雑化する現代においては、目視検査や基本的な分析だけでは限界があるため、CAE受託解析の導入が有効です。CAE技術を活用することで、問題の根本原因を特定し、再発防止策を効果的に講じることができます。
お気軽にご相談ください
製品不良の原因調査やCAE受託解析に関してご不明な点やご相談がありましたら、ぜひご連絡ください。
豊富な経験を持つ解析エンジニアがニーズに合った最適なソリューションを提案します。